Testing Equipment
Precision in Quality: Advanced Inspection Equipment in a Professional Glass Bottle Factory
As a professional glass bottle factory supplier, ensuring the highest standards of quality is our utmost priority. From creating visually appealing designs to guaranteeing structural integrity, every bottle must meet stringent quality requirements before reaching the hands of consumers. This level of precision is achieved through state-of-the-art inspection equipment and dedicated human expertise.
In this article, we will explore the key inspection processes in a glass bottle factory, including stress testing, leak detection, and manual inspection, emphasizing how these methods ensure superior products for our clients.
1. Stress Testing Equipment: Ensuring Durability and Reliability
Stress testing equipment plays a pivotal role in assessing the strength and resilience of glass bottles. This is essential for products like beverage bottles, perfume containers, and jars that must endure various handling conditions during transportation and use.
How It Works
Polariscopes
Polariscopes are used to detect residual stress within the glass. By analyzing how light passes through the material, these devices reveal stress points that may compromise the bottle's durability.
Thermal Stress Testers
These machines simulate extreme temperature changes to ensure the bottle can withstand conditions like hot filling, refrigeration, or microwave use.
Pressure Resistance Equipment
For bottles designed to hold carbonated beverages or pressurized contents, pressure testing machines are employed to verify their ability to withstand internal forces.
Advantages
Identifies hidden weaknesses in the glass structure, reducing the risk of breakage during use.
Ensures compliance with industry standards for strength and safety.
Builds consumer trust by guaranteeing a robust and reliable product.
By integrating advanced stress testing equipment, factories can deliver glass bottles that meet the demanding expectations of global markets.
2. Leak Detection Equipment: Guaranteeing Product Integrity
Leak detection is another critical aspect of quality control in glass bottle manufacturing. Whether the product is a perfume bottle, an essential oil container, or a beverage bottle, even a tiny leak can lead to significant product loss and customer dissatisfaction.
How It Works
Vacuum Leak Testers
These machines create a vacuum around the bottle to detect air escaping through micro-cracks or imperfections in the glass.
Pressure Leak Testers
Pressure is applied internally to the bottle to identify weak points that might allow liquid to seep through.
Ultrasonic Leak Detectors
Advanced systems use sound waves to locate the smallest leaks, ensuring unmatched precision.
Advantages
Prevents product contamination and waste by ensuring airtight sealing.
Minimizes customer complaints and returns due to leaking bottles.
Enhances the brand's reputation for quality and reliability.
By employing sophisticated leak detection equipment, factories can safeguard the functionality and aesthetic appeal of their glass products.
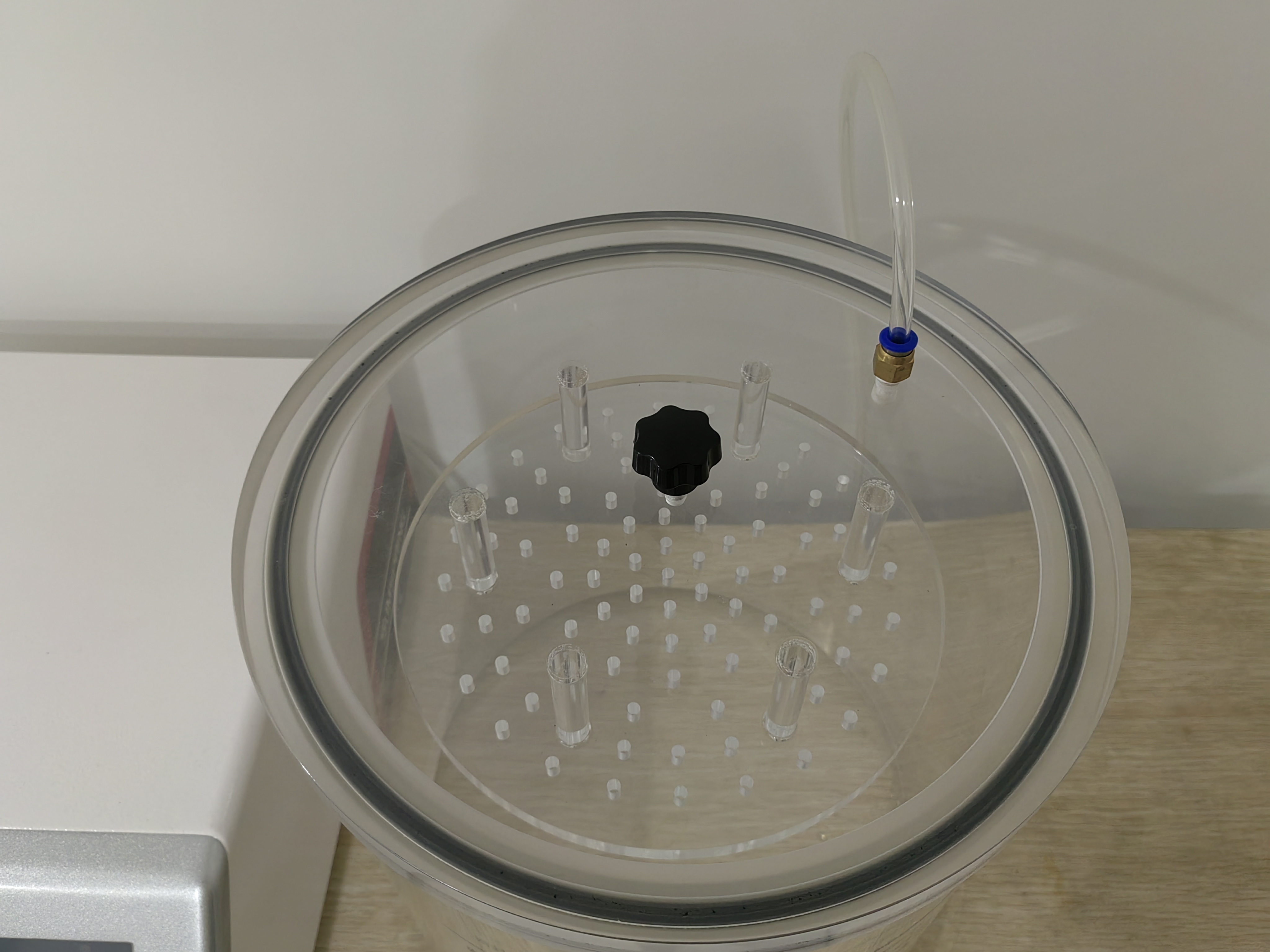
Leak Tester Leak Testing Equipment-1
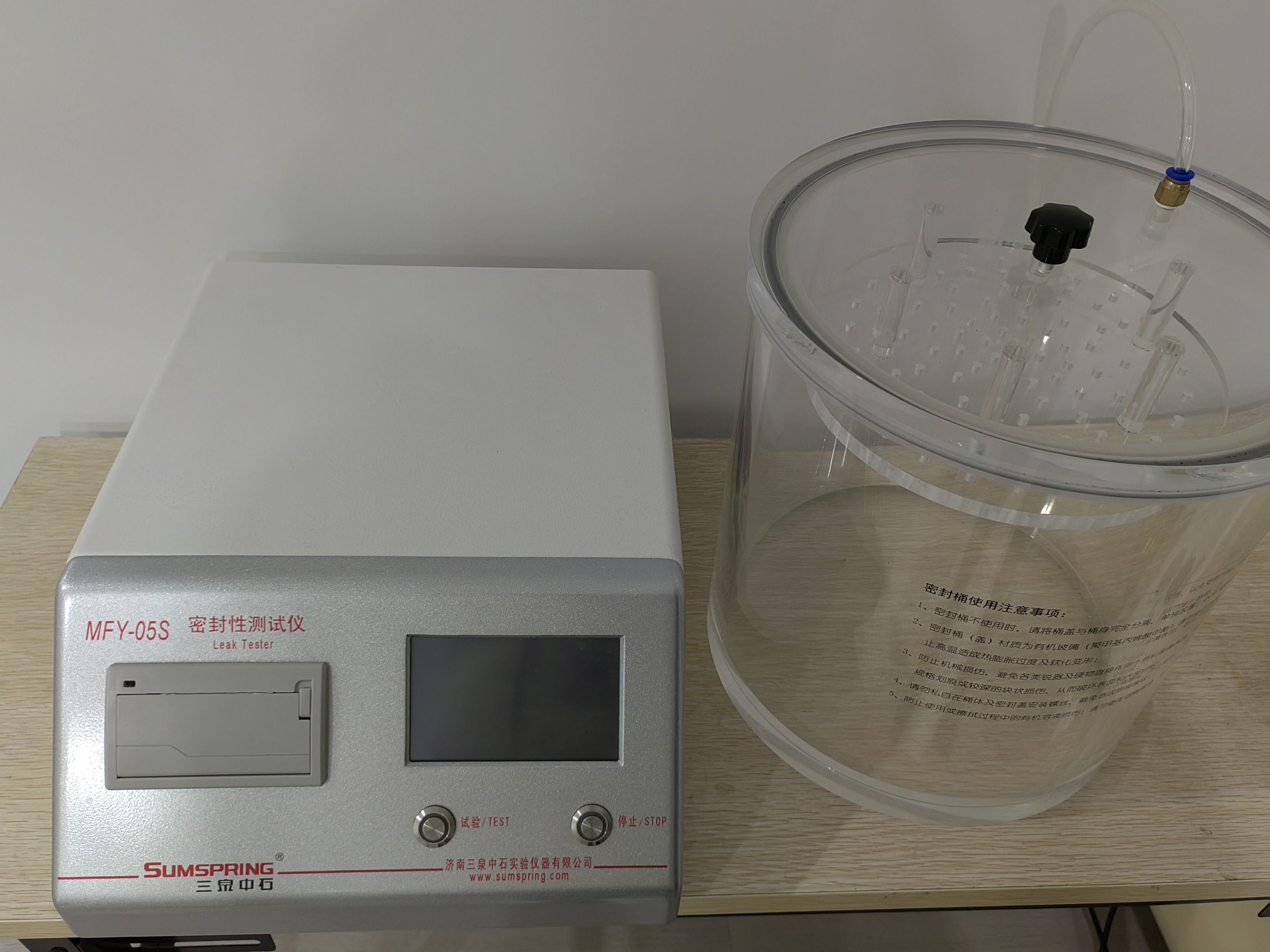
Leak Tester Leak Testing Equipment-2
3. Manual Inspection: The Human Touch in Quality Control
While automated systems are invaluable for high-speed and consistent inspections, the human eye and hand remain irreplaceable for certain quality checks. Manual inspection adds an additional layer of assurance, particularly for premium products where aesthetics and detail are paramount.
How It Works
Surface Inspection
Trained workers carefully examine each bottle for cosmetic defects such as scratches, bubbles, or irregularities in shape.
Functional Tests
Inspectors verify key features like bottle threading, neck dimensions, and overall fit for caps or closures.
Custom Requirements
For customized orders, manual checks ensure that every bottle adheres to the client’s unique specifications, from logos to decorative finishes.
Advantages
Detects subtle flaws that automated systems might miss, especially in complex designs or specialty finishes.
Allows for on-the-spot adjustments, ensuring faster resolution of production issues.
Demonstrates a commitment to quality through meticulous attention to detail.
Manual inspection complements automated systems, offering a comprehensive approach to quality control.
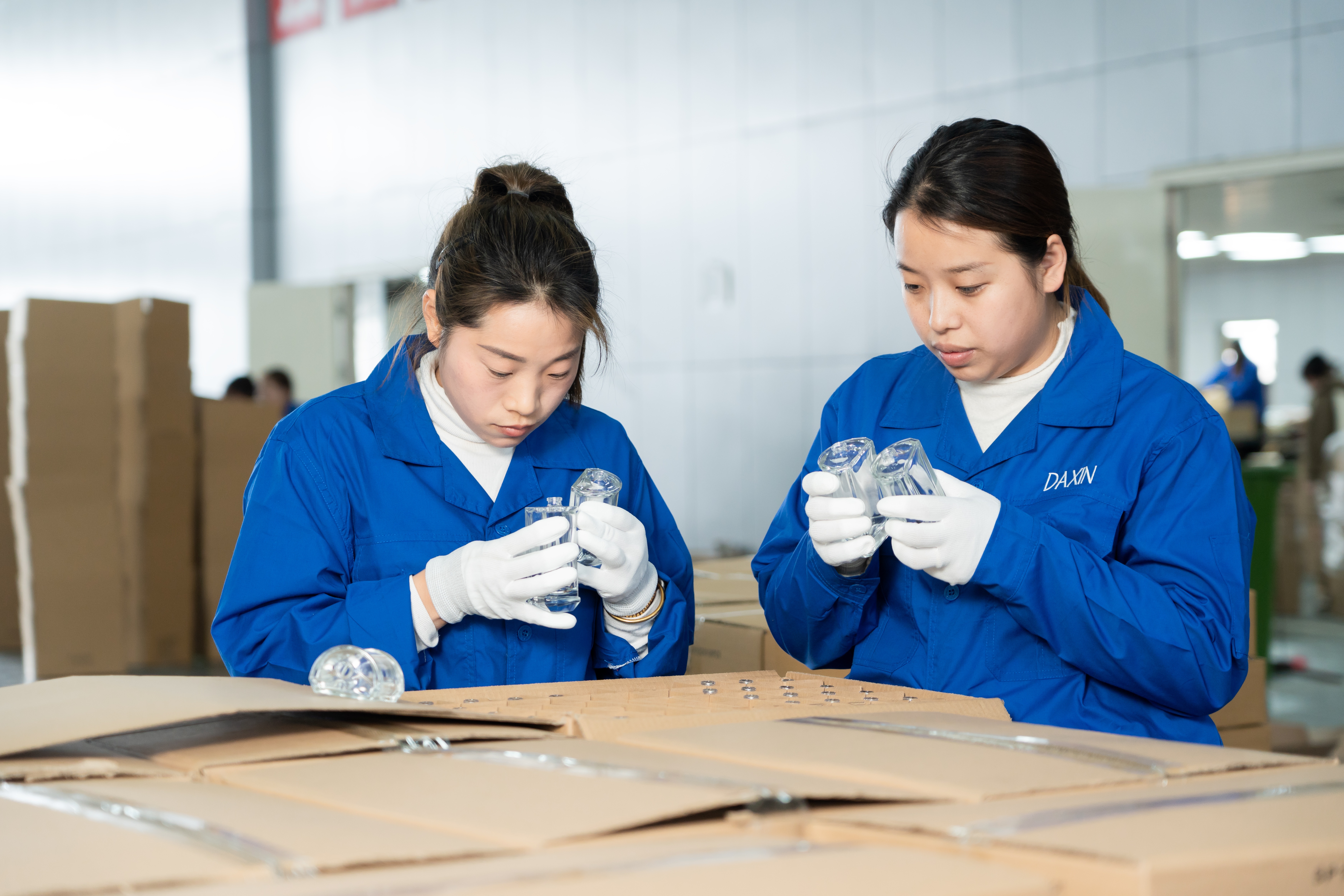
Test-1
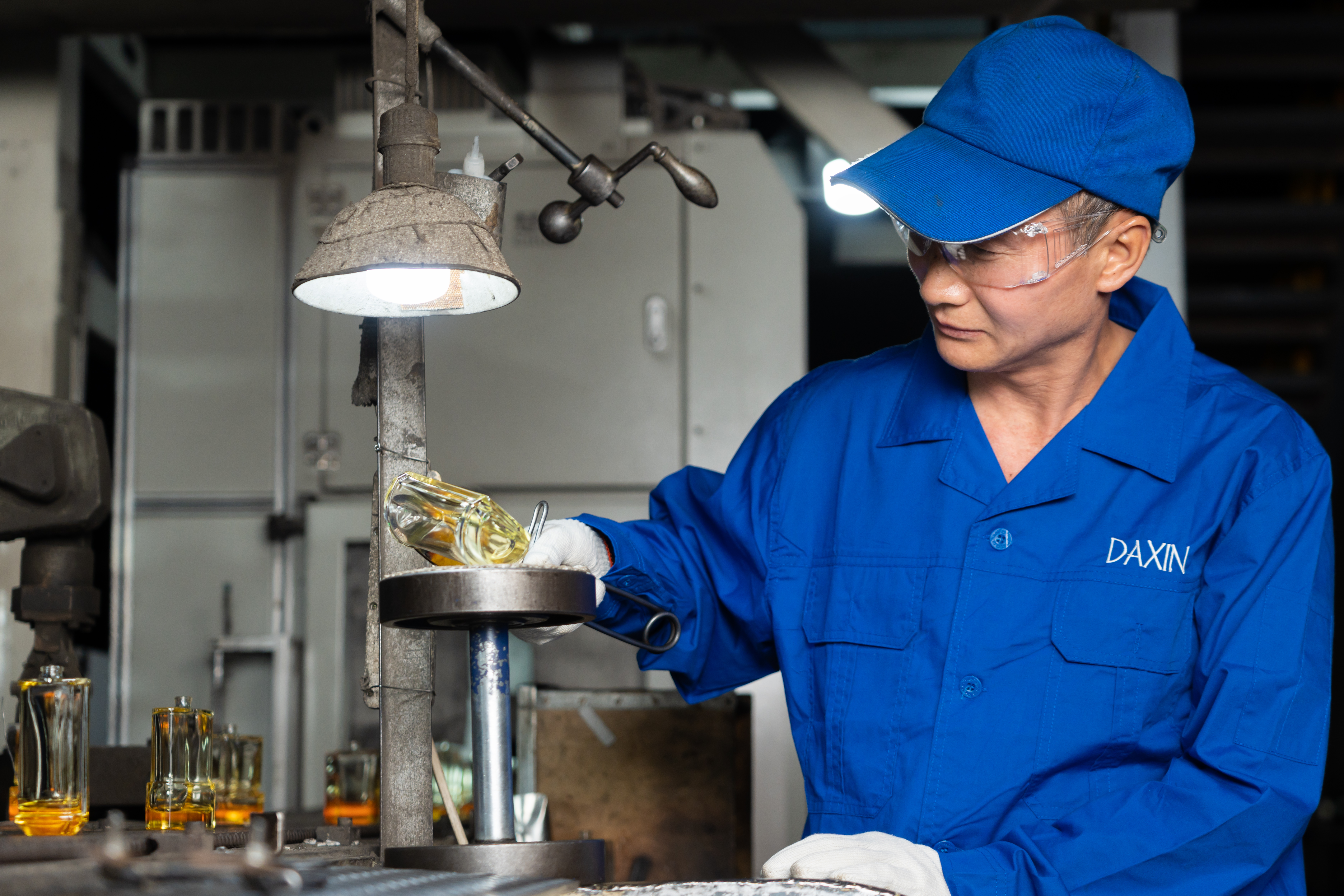
Test-2
The Synergy Between Technology and Expertise
The combination of advanced equipment and human expertise ensures that every glass bottle leaving the factory is flawless. Here’s how this synergy works:
1. Early Detection
Stress testing equipment identifies structural issues at the beginning of production, preventing costly errors later.
2. Functional Assurance
Leak detection systems verify the bottle's usability, safeguarding both the product and the end-user experience.
3. Final Perfection
Manual inspections ensure the bottle’s aesthetics and functionality meet the highest standards before packaging and delivery.
Investing in Quality for Our Clients
As a leading glass bottle supplier, our commitment to quality extends beyond equipment. We continually invest in cutting-edge technology and train our workforce to maintain rigorous inspection standards. These efforts translate into tangible benefits for our clients:
Consistency
Every bottle meets precise specifications, ensuring uniformity across batches.
Reliability
Thorough testing minimizes the risk of defects, boosting customer confidence in your products.
Customization
From stress resistance to flawless branding, our inspection processes support tailored solutions for diverse market needs.
Conclusion: A Commitment to Excellence
The success of a professional glass bottle factory lies in its dedication to quality. By leveraging advanced stress testing equipment, leak detection systems, and meticulous manual inspections, we ensure that every bottle meets the highest standards of durability, functionality, and visual appeal.
For clients, this commitment translates into exceptional products that enhance brand value and deliver unparalleled customer satisfaction. Whether you need sturdy beverage containers or elegant perfume bottles, our factory is equipped to turn your vision into reality. Trust in our expertise, and let our inspection excellence become the foundation of your success.