Production Equipment
The Backbone of a Professional Glass Bottle Factory:
Equipment That Defines Excellence
When it comes to producing high-quality glass bottles, the cornerstone of any professional factory is its equipment. From precision mold-making to advanced decorating techniques, every step in the manufacturing process relies on sophisticated machinery. This article provides an in-depth look at the key equipment used in a professional glass bottle factory, including inspection tools, bottle-making machinery, coating lines, screen printing equipment, and molds.
1. Inspection Equipment: Ensuring Quality at Every Step
Inspection equipment is the first and last line of defense in guaranteeing flawless products. Advanced factories employ a range of automated and manual inspection tools to detect defects in shape, surface, and structural integrity.
Automated Visual Inspection Systems
These systems use cameras and sensors to identify imperfections such as cracks, bubbles, or uneven surfaces. They ensure every bottle meets strict industry standards.
Pressure and Thermal Resistance Testers
These machines verify that bottles can withstand internal pressure and extreme temperatures, critical for products like carbonated beverages or perfumes.
Thickness Gauges
High-precision tools measure glass thickness to ensure uniformity, improving the bottle's strength and aesthetic appeal.
By integrating these technologies, factories achieve near-zero defect rates, providing customers with reliable and high-quality products.
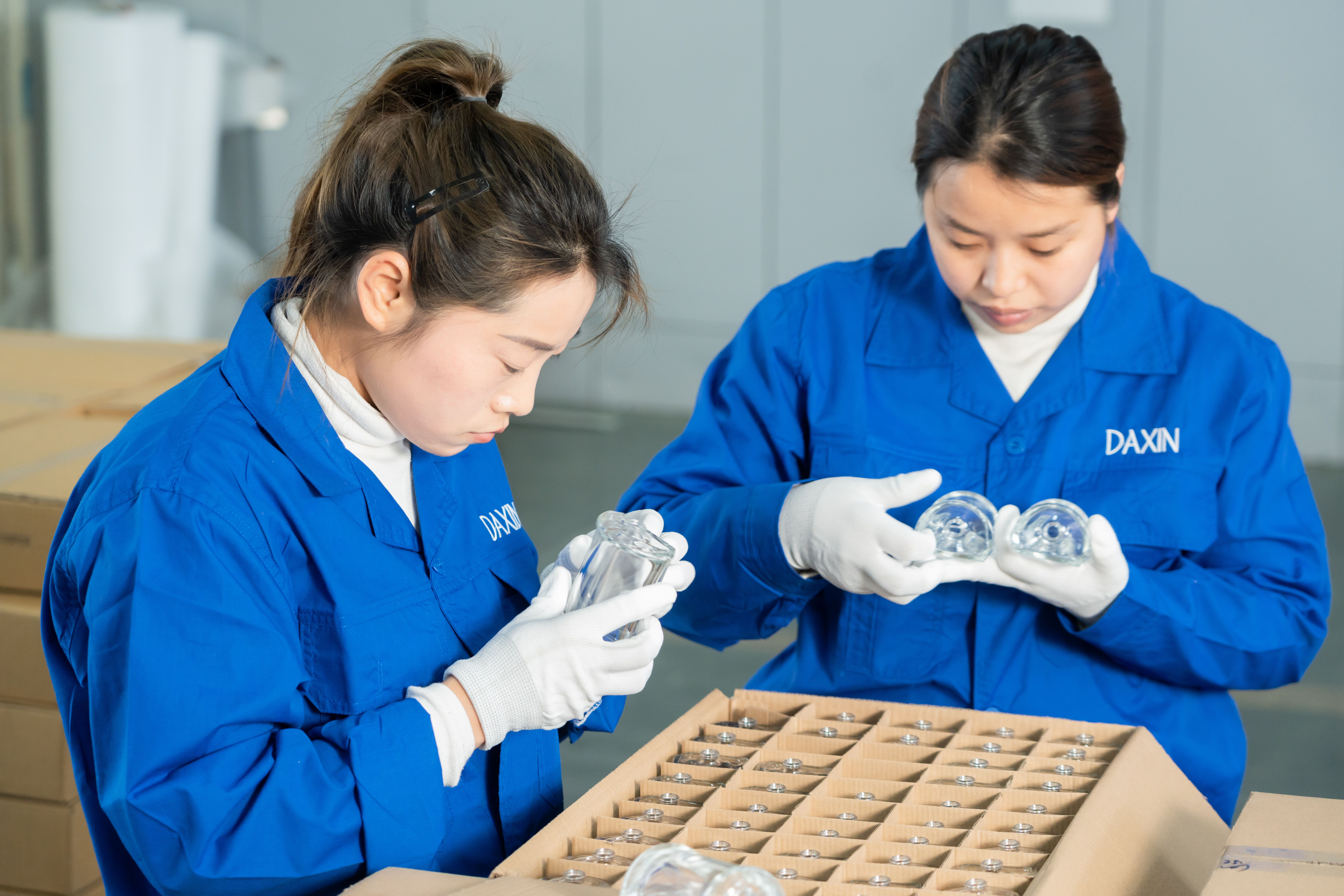
Manual detection-1
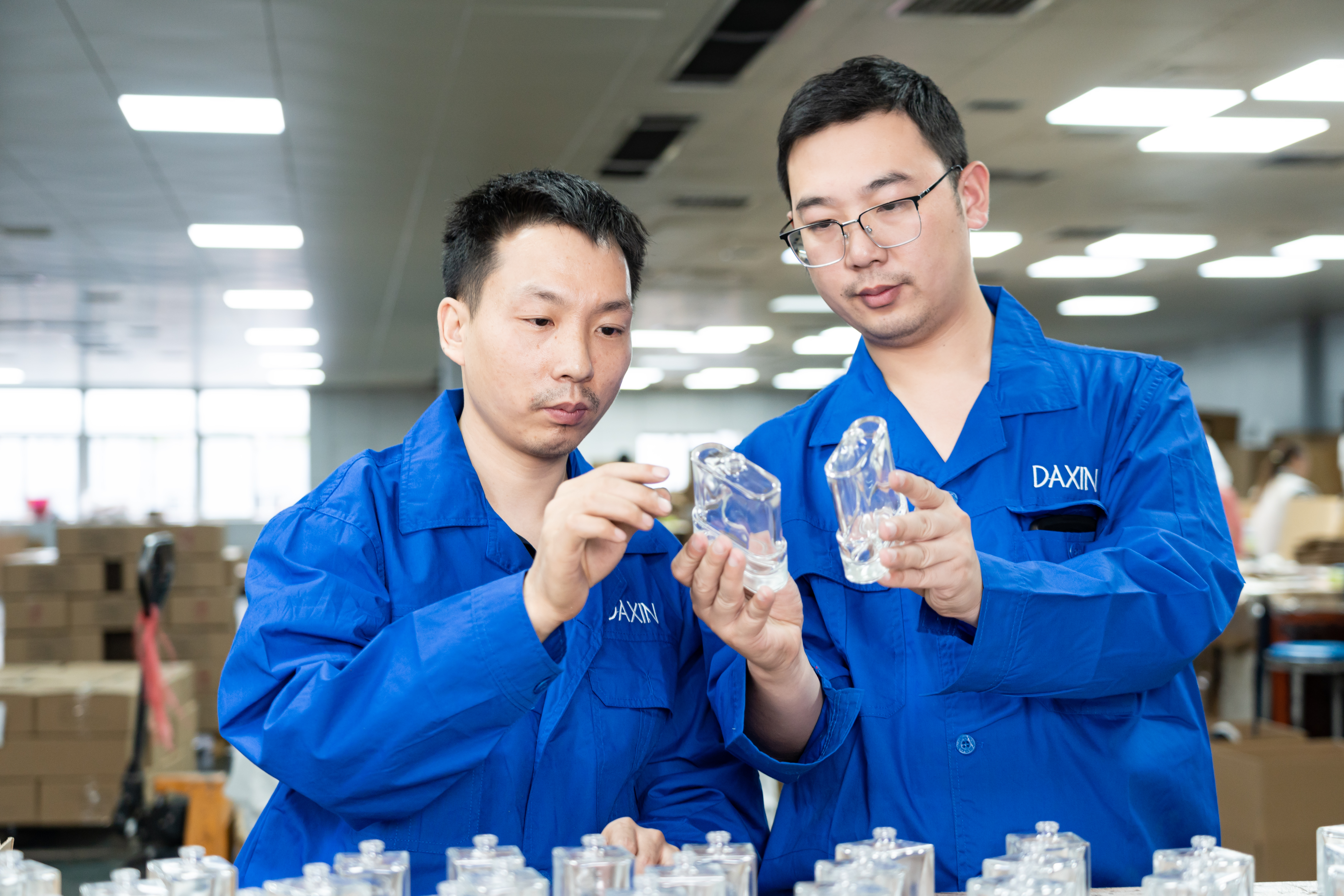
Manual detection-2
2. Bottle-Making Equipment: The Heart of Production
Glass bottle production begins with high-tech bottle-making equipment, which transforms raw materials into beautifully crafted bottles.
Automatic IS (Individual Section) Machines
These machines are the industry standard for efficient bottle production. They mold glass into precise shapes and sizes through a combination of blow-and-blow, press-and-blow, or narrow neck press-and-blow processes.
Advanced Melting Furnaces
Energy-efficient furnaces ensure a consistent glass melt, enabling smooth production and minimizing environmental impact.
Batching and Feeding Systems
Automated systems mix raw materials like silica sand, soda ash, and limestone in precise ratios, ensuring high-quality molten glass for production.
State-of-the-art bottle-making equipment not only ensures accuracy but also enables high-speed production, meeting the demands of global markets.
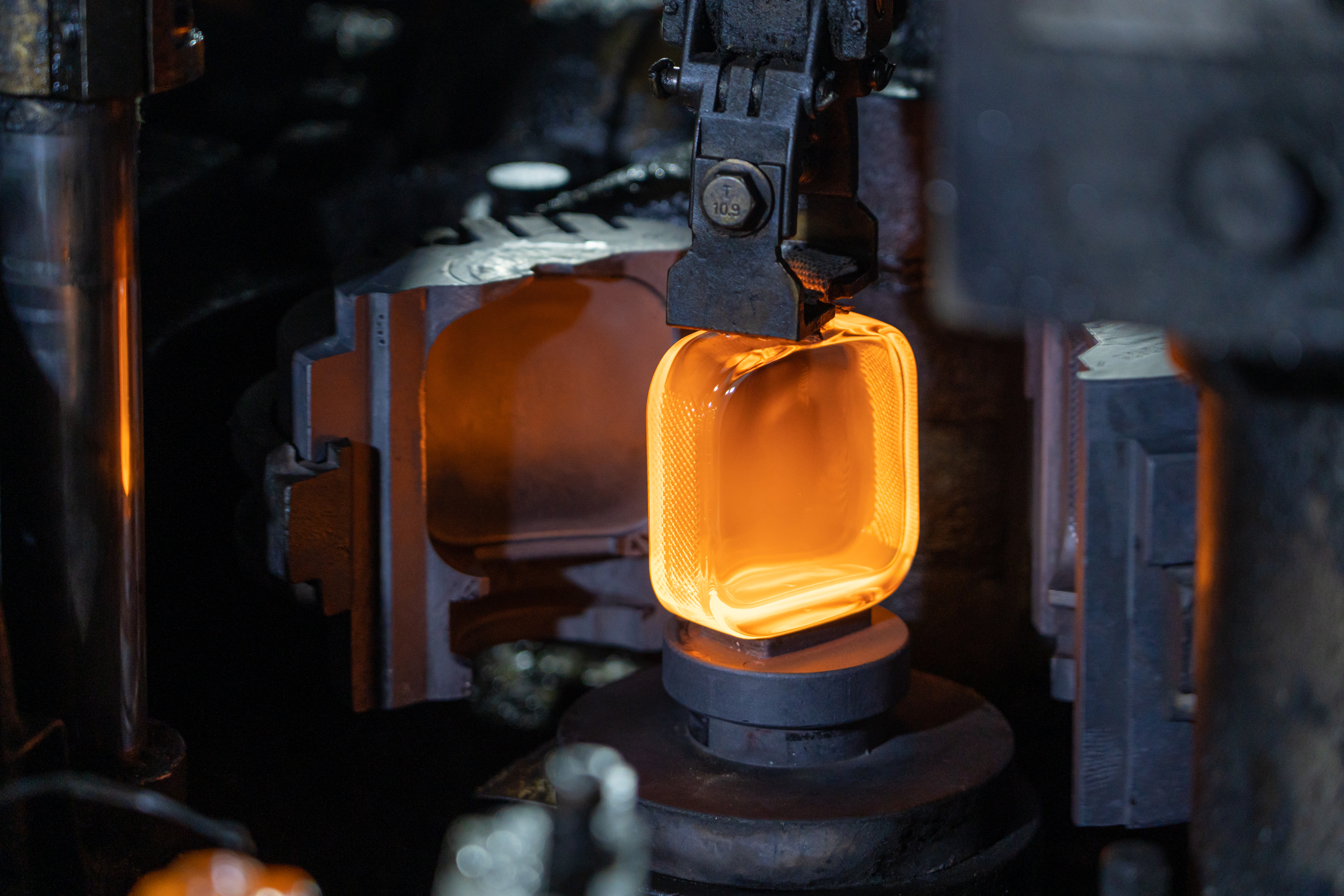
Bottle making equipment-1
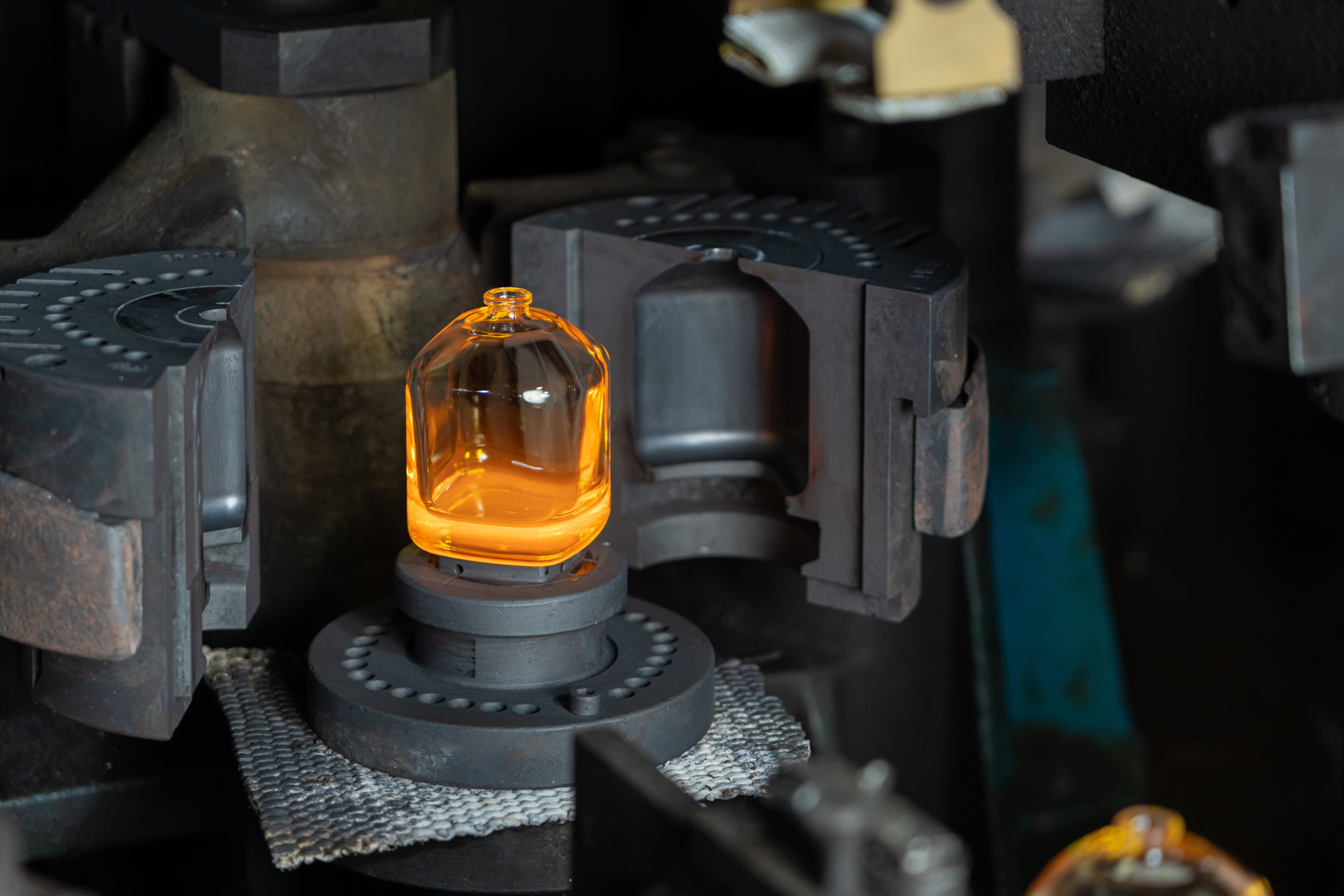
Bottle making equipment-2
3. Coating and Spray Lines: Adding Color and Protection
To meet diverse customer preferences, many factories incorporate advanced spray coating lines to enhance the appearance and functionality of glass bottles.
Automated Spray Booths
These booths evenly apply coatings in a wide range of colors and finishes, from matte and glossy to metallic and frosted.
UV and Thermal Curing Systems
After spraying, curing systems harden the coatings, ensuring durability and resistance to scratches or chemical interactions.
Gradient and Pattern Spray Technology
For premium products, specialized systems can create gradient effects or intricate patterns, adding a luxurious touch to the bottles.
Modern coating lines not only provide aesthetic enhancements but also protect the glass surface, ensuring a longer lifespan for the product.
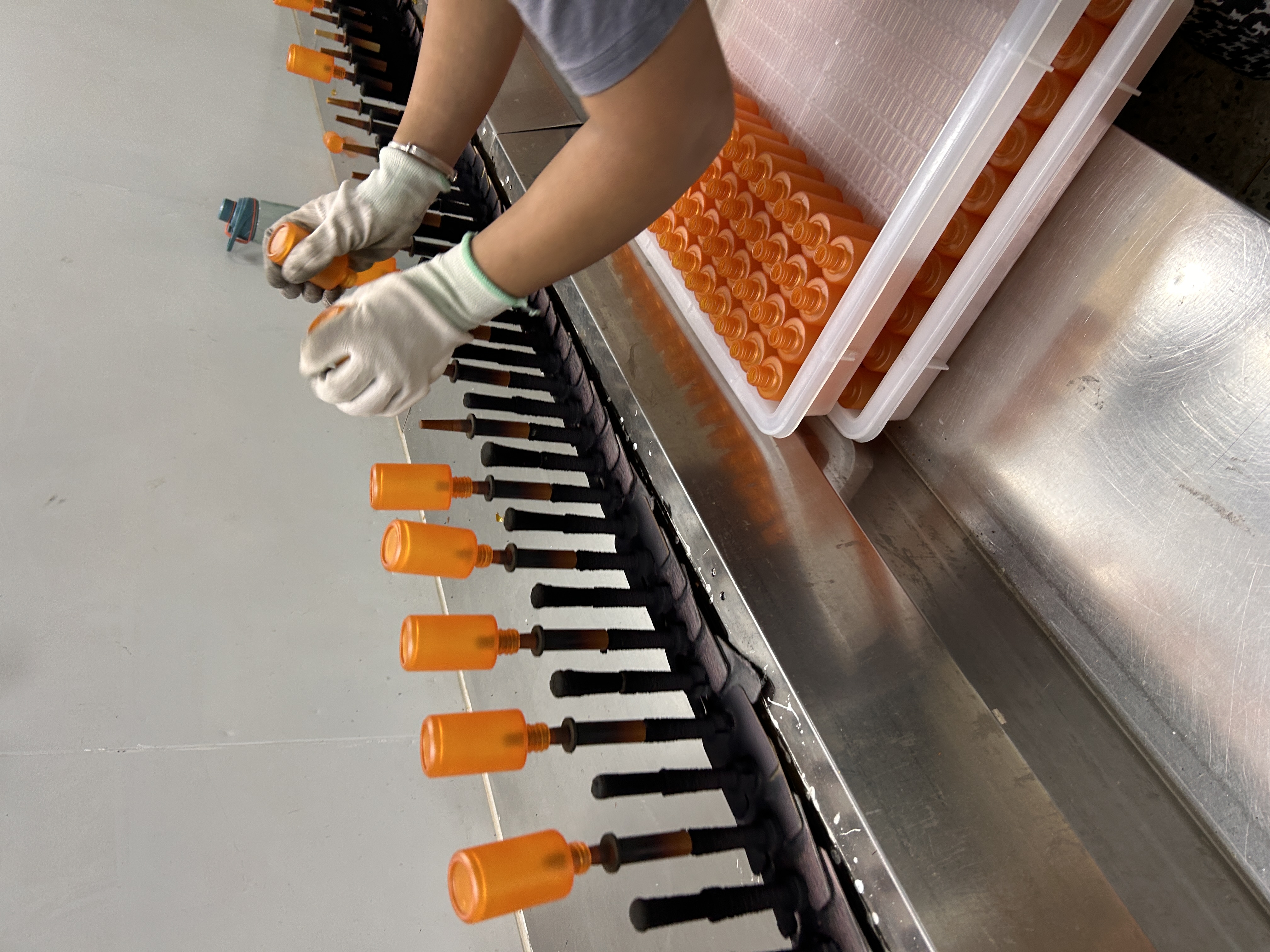
Spraying technology-1
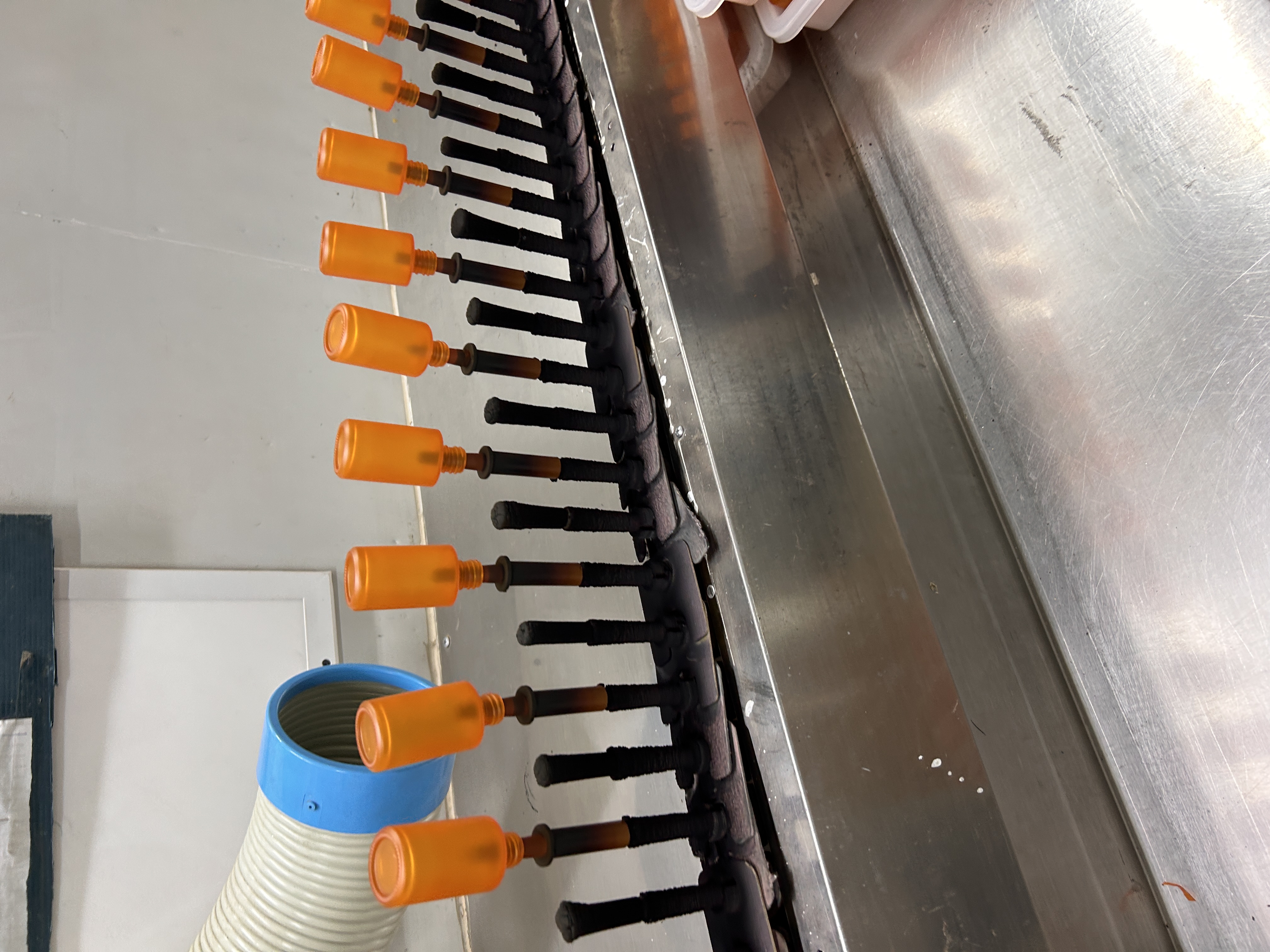
Spraying technology-2
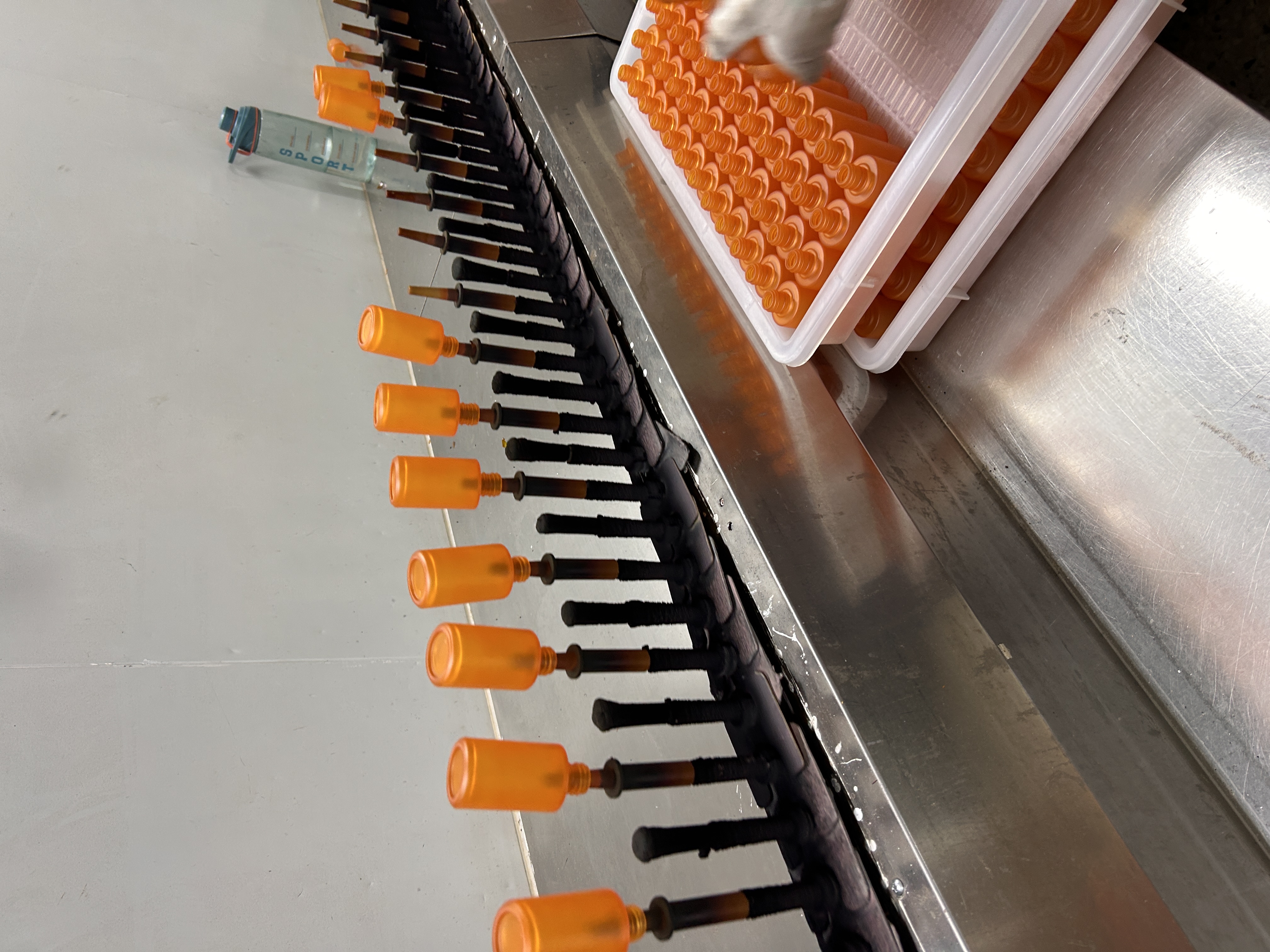
Spraying technology-3
4. Screen Printing Equipment: Turning Bottles into Art
Screen printing is an essential step in branding and decorating glass bottles, transforming them into eye-catching marketing tools.
Multi-Color Screen Printers
These machines apply detailed and vibrant designs directly onto the glass surface using ceramic or organic inks.
UV and Infrared Drying Systems
Once printed, advanced drying systems cure the inks for long-lasting adhesion, even on curved or textured surfaces.
High-Speed Automated Printing Lines
With capabilities to print thousands of bottles per hour, these systems combine speed with precision, ideal for large-scale production.
Screen printing equipment allows factories to offer customizable designs, meeting the unique branding needs of their clients.
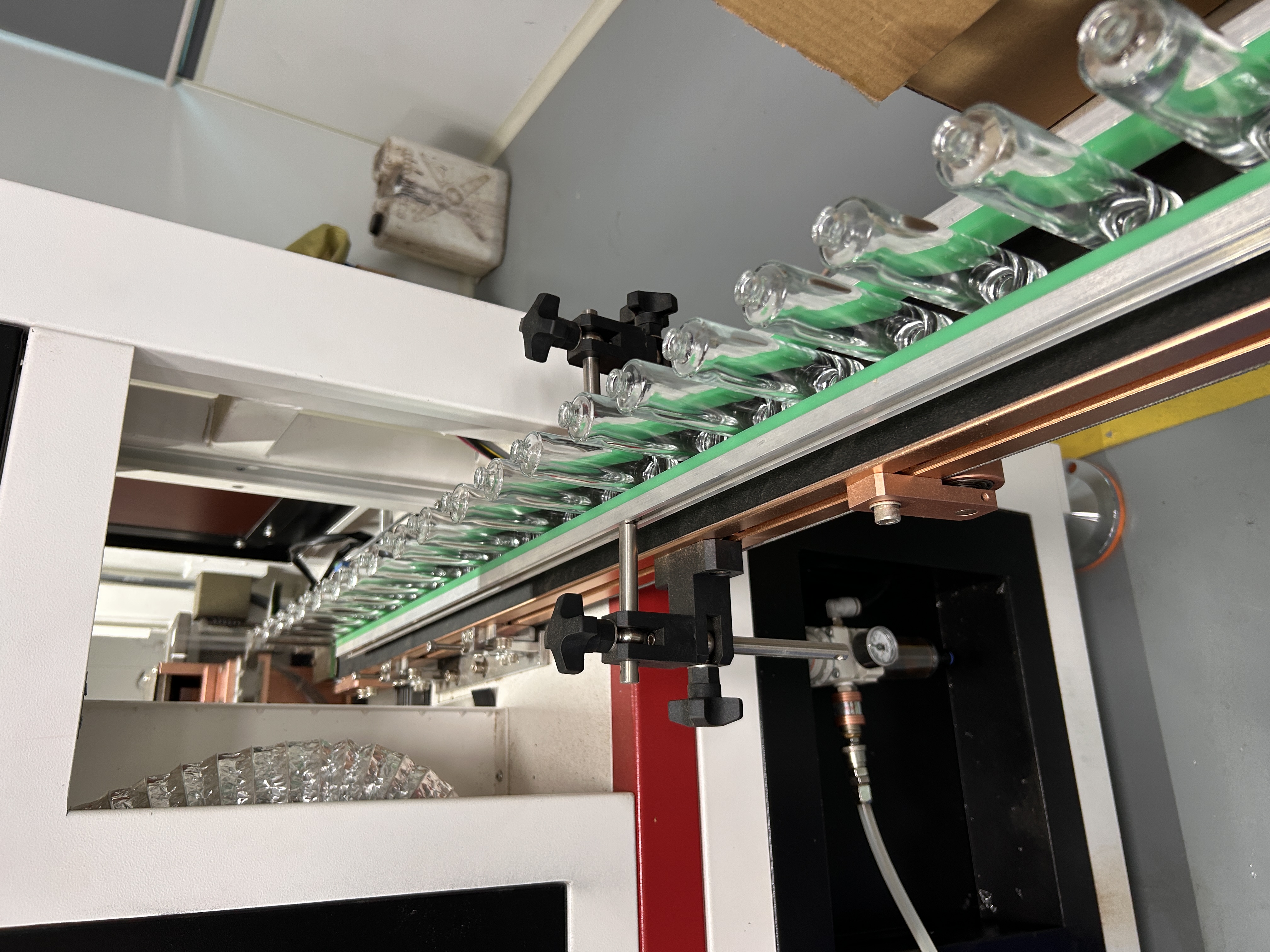
Silk screen printing-1
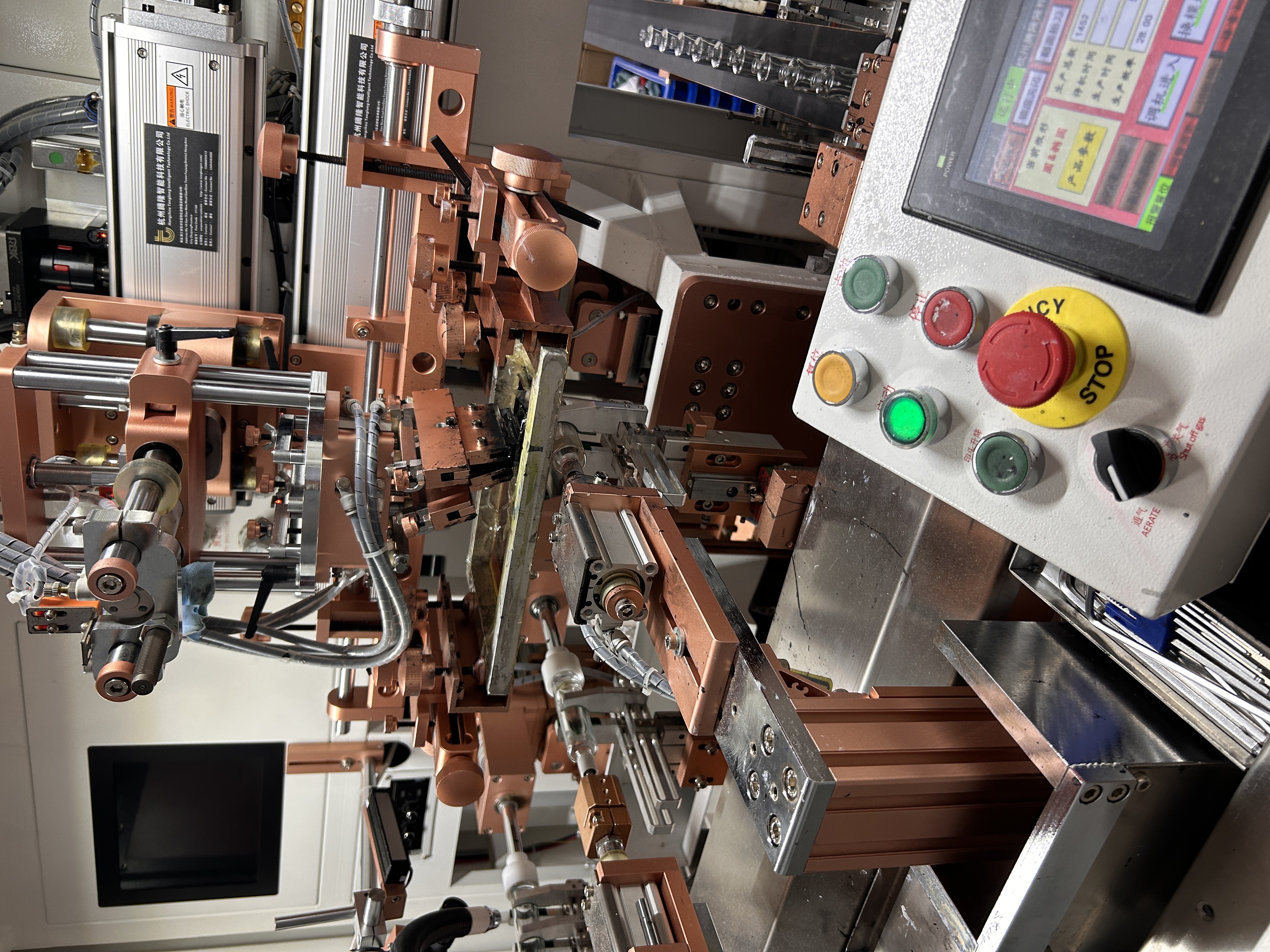
Silk screen printing-2
5. Molds: The Blueprint of Precision
No glass bottle can exist without molds, which define its shape, size, and intricate details. The quality of molds directly impacts the final product, making them a critical component of the manufacturing process.
CNC Precision Mold-Making Machines
These machines create molds with exceptional accuracy, ensuring consistent results across large production runs.
High-Quality Mold Materials
Factories use materials like cast iron or alloy steel for durability and heat resistance, enabling long-lasting performance under extreme conditions.
Custom Mold Design Capabilities
With advanced software, factories can design molds tailored to specific customer requirements, offering unparalleled customization options.
High-quality molds ensure that every bottle is a perfect reflection of the brand's vision, whether it's a perfume bottle, beverage container, or candle jar.
Mold-1
Mold-2
6. The Role of Automation in Modern Glass Bottle Factories
The integration of automation across all equipment types has revolutionized glass bottle manufacturing. Automated systems streamline operations, reduce labor costs, and minimize errors, ensuring consistent quality. From robotic arms on the production line to AI-powered quality control systems, automation enables factories to meet the demands of fast-paced markets without compromising on standards.
Conclusion: Equipment as a Competitive Advantage
A professional glass bottle factory's success lies in its equipment. High-quality machinery ensures precision, efficiency, and flexibility, enabling factories to deliver superior products tailored to their clients' needs. By investing in advanced inspection tools, bottle-making machines, coating lines, screen printing systems, and custom molds, these factories set the gold standard in the industry.
For businesses seeking a reliable glass bottle supplier, choosing a factory with cutting-edge equipment is essential. Not only does it guarantee product quality, but it also ensures the ability to meet unique and evolving market demands. Whether it's a sleek perfume bottle, a decorative aroma diffuser, or a functional beverage container, the right equipment transforms ideas into reality, making every glass bottle a masterpiece.